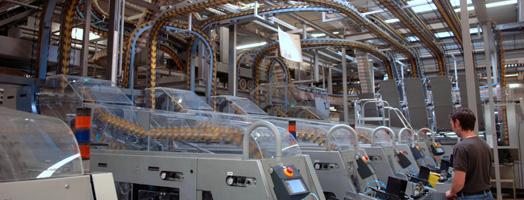
Manufacturing
HOW LEAN SIX SIGMA IMPROVES MANUFACTURING
Manufacturing is where Lean and Six Sigma all began. The incredible success of the two methodologies is a testament to their effectiveness in generating productivity gains with cost reductions and quality improvements. During this time, Lean and Six Sigma have proven not to be a fad, but rather a key to competitiveness in today’s marketplace.
While both methodologies produce great results when employed separately, the integration of the two – when done properly – creates a powerful combination for implementing process improvement.
Lean’s strengths are to simplify processes and reduce manufacturing cycle times by removing steps from processes that do not add value to the product and providing tools to improve flow. In short, Lean means speed. Alternately, Six Sigma handles more complex issues with a problem-solving tool that seeks out causes of defects with a powerful roadmap called DMAIC – define, measure, analyze, improve, control. Driving variation out of processes is the key to reducing defects.
Ultimately, Six Sigma has a goal of achieving a near perfect 3.4 defects per million opportunities. It has a strict approach to controlling and sustaining improvements. Together, these two methodologies achieve significantly reduced cycle times and higher quality simultaneously. For these reasons, Lean Six Sigma is the toolbox of choice among manufacturers who have a passion for continuous improvement.
For more information about our consulting and training services for Lean Six Sigma in Manufacturing, contact us.
Follow Us: