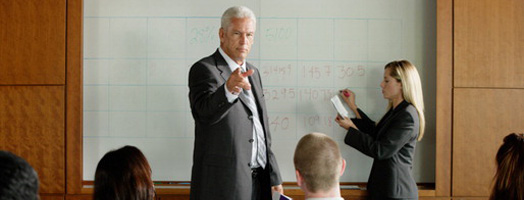
BASIC PROBLEM SOLVING AND PROCESS IMPROVEMENT
Course Length: 2 days
In this course, the participant will learn basic problem solving tools and skills such as root cause analysis, cause and effect diagrams, the 5 whys and basic data analysis techniques. This hands-on course covers some of the basic problem solving tools typically taught in a Lean Six Sigma Green Belt course. As part of the training, each participant is required to identify and develop a plan to improve at least one process in their organization. The training incorporates a simulation to enable participants to practice applying the tools. Participants are required to brief their leadership on their plan with expected outcomes and metrics for success.
Course Objectives
- Know how to identify and select the pertinent business problems
- Be able to write an effective problem statement
- Be able to determine the starting and ending process points of a given problem
- Gain experience using basic quality tools
- Know how to effectively measure process changes
Primary Topics
- Prioritizing Problems
- Generating Effective Problem Statements
- Effective Scoping
- Basic Quality Tools
- Measuring Impact
For more information about this course please call 1.855.NOVACES or click here to contact us by email.
Follow Us: